
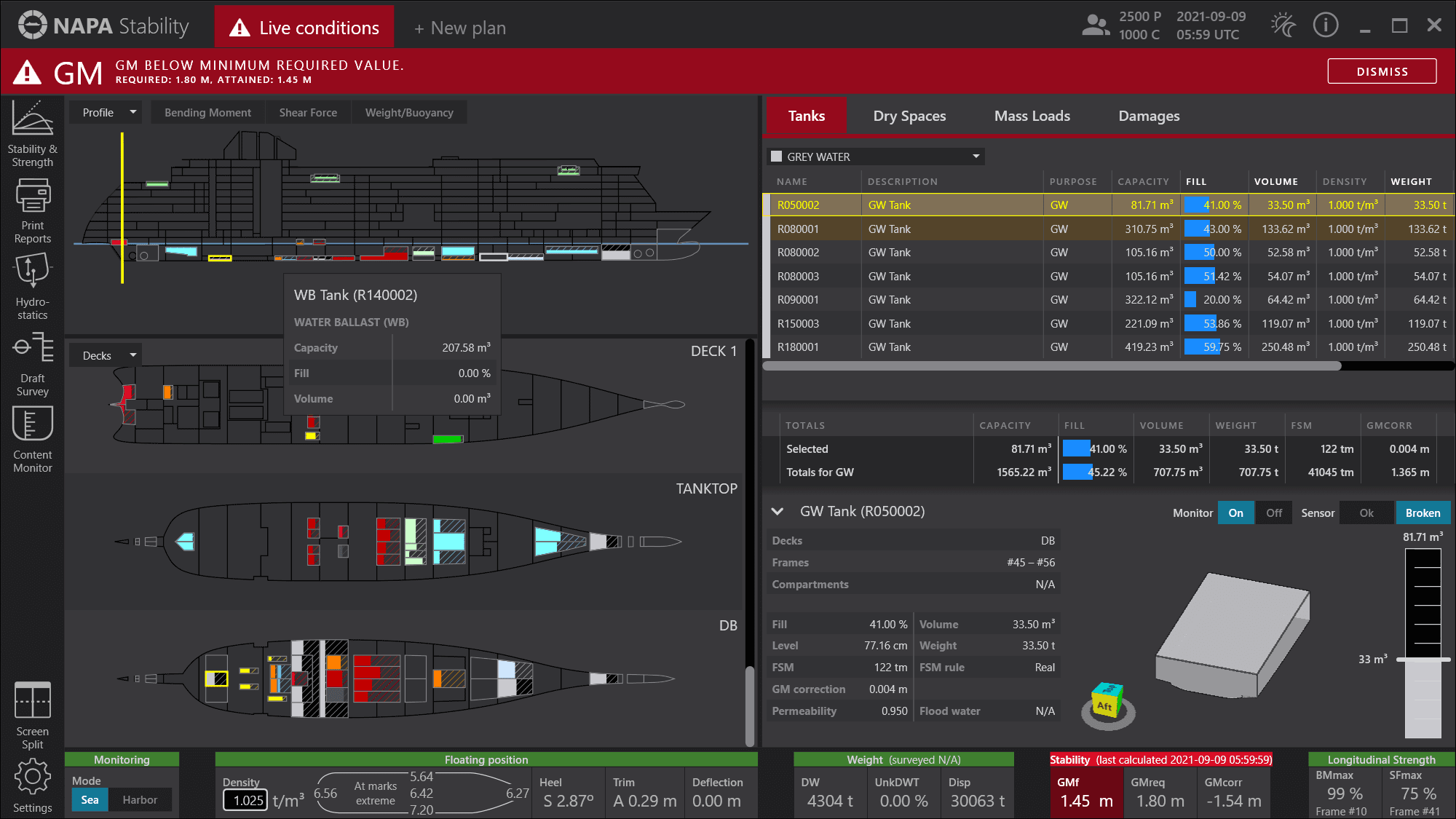
Green ship technologies are gaining in importance in diverse areas of ship design. The present study validates the effectiveness of the proposed hydrodynamic optimization procedure, ushering in process automation and performance improvement in practical ship design practices. The ultra-large containership was built and delivered to the ship owner. Improvements of ship performance achieved by the proposed F-Spline procedure are demonstrated through numerical experiments and through correlations with experimental data.
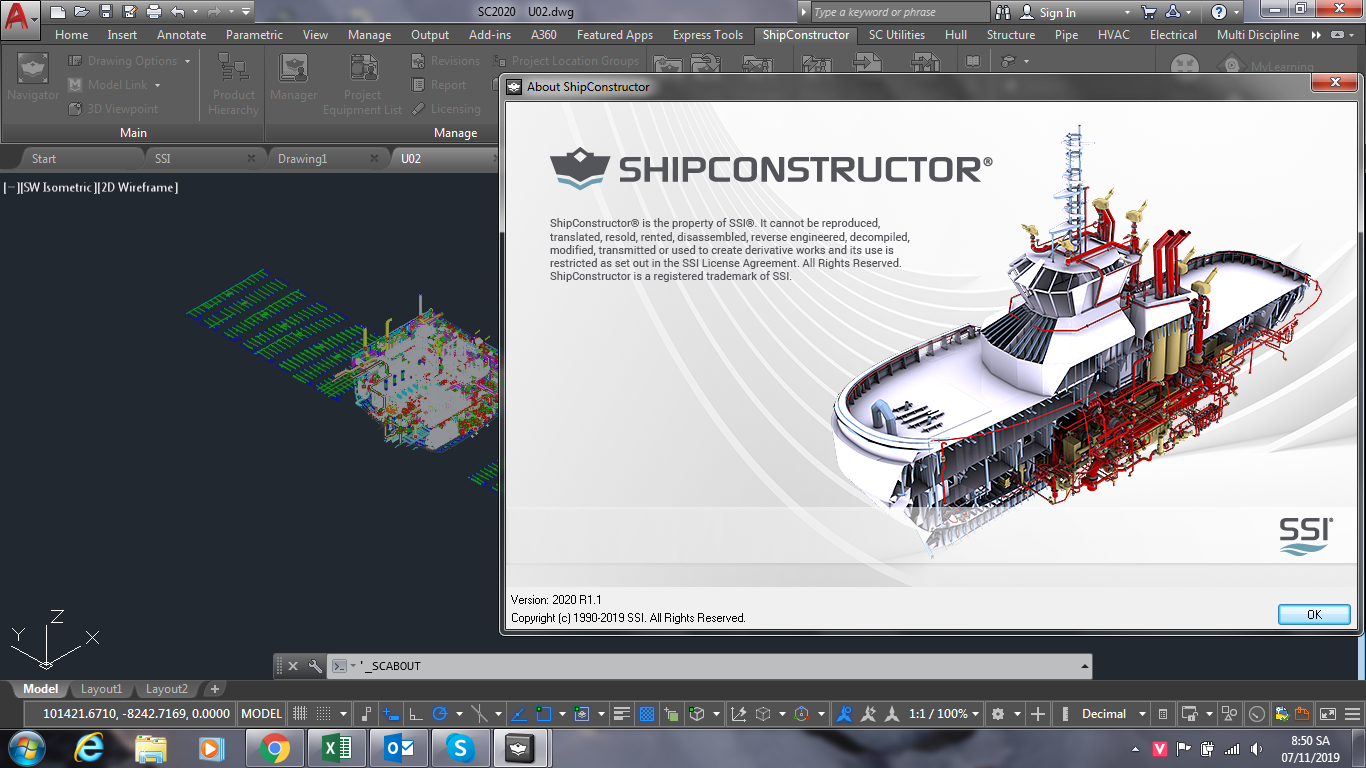
The present F-Spline based optimization procedure is applied to two distinct hydrodynamic hull form optimizations: the global shape optimization of an ultra-large container ship and the forebody hull form for the hydrodynamic optimization of an LPG carrier. Two functionalities of the parametric geometry models are used in the present study: a constrained transformation function to account for hull form variations and a geometric entity used in full parametric hull form design. Hydrodynamic optimizations of ship hull forms have been carried out employing parametric curves generated by fairness-optimized B-Spline form parameter curves, labeled as F-Spline.
